Router/Plasma Cutting
what is Plasma cutters?
Plasma cutters are commercially accessible metal-working machines that can cut through many types of metals in a single run of operation. These machines are available in a variety of thickness-cutting capabilities and frequently approximate the appearance and size of a small wire-feed welder. Once the plasma arc for the cut is generated, compressed air is utilized to blow the molten metal through the cut, creating the cutting kerf. CNC plasma tables are frequently compared to CNC routers. The spoil board has been replaced with a metal grid-work, and the spindle head has a plasma torch added, which are the only visible differences.
An initial pierce height for the material is used to puncture through the metal stock, similar to setting a tooling touch off in a routing or milling process. Once established, an auxiliary form of controller device known as a torch height controller (or THC) continuously samples the voltage potential between the tip and the material being cut to maintain the right torch tip distance from the substance. The rationale for regularly sampling the tip voltage and making subsequent modifications is because metal warps as it is cut (especially thinner materials); not all metal sheet stock rests level on the table top, and a consistent distance between the torch tip and material must be maintained. Furthermore, many sheet metals are originally corrugated rather than flat, therefore another role of the THC is to track irregular-shaped material.
The motion controller hardware and software control both the X and Y axes for two-dimensional motions during regular cutting operation, but the THC controls the Z axis for vertical adjustments. The physical link for the THC type of device to the computer and controller software is often through a second parallel connection. As a result, two db-25 connections are often required: one for the motion controller and the other for torch height control.
In the same way that a controller database may hold tooling information, numerous parameters such as material type, thickness, feed rates, and plasma-cutting parameters are often kept in a database file for simple reference with plasma operations.
FIGURE 1-2 Torch height controller
Shops are frequently involved in the manufacturing of materials that can benefit from the usage of both a router and a plasma table. Invariably, the question of whether to utilize a single table for each of these sorts of operations emerges. It is advised to avoid utilizing a single CNC table for both operations for the following reasons: The spoil board table is expected to be precisely flat (or orthogonal) with reference to the Z axis by a CNC router table. There is no spoil board for usage with plasma, but rather an open support framework for the molten metal to travel through during the torch operation. As a result, dismantling and reinstalling a flattened spoil board each time you change cutting procedures would be complex and time consuming.
Placing a spoil board on top of the plasma grid does not guarantee a flat and level surface, and it must be surfaced (i.e., fly cut) each time it is moved.
It is very possible to take a current CNC router and replace its application with a plasma torch, as is frequently done. If you are building or purchasing a plasma table, keep in mind that the table’s mass and strength do not need to be those of a router, as little to no force is met during a plasma (or laser, water jet, etc.) cutting operation, as opposed to routing or milling. Sound Logic, Inc. manufactures the complex THC controller illustrated in Fig. 1-2, which is also utilized on the plasma table detailed in Chapter 11 on Building Your Own CNC Plasma Table. This equipment is highly recommended for anybody looking for a new or retrofit plasma cutting machine.
first you need to know some methods and tools.
Methods of Holding Down
The spinning moving bit exerts forces on the material being worked on when conducting rotary cutting. To counteract these stresses, there are numerous methods for securely holding the work material in place. Although any of the hold-down methods listed below will work, they may not be the best choice in every situation. It is the user’s obligation to select and employ a hold-down technique that is suitable and safe for the cutting work at hand. Using your hands to hold material in place during a cutting process is never an option.

Mini hold down clamp
Vacuum
Vacuum hold-down is a popular approach, especially when fullsheet stock is the principal material being dealt with. When dealing with full-sheet plywood, common industries include woodworking and furniture building. Full sheets of plastics, composites, and thin metal sheeting are also used in the signs sector. The vacuum pressure is produced using a device known as a regenerative blower. These blowers are enormous and noisy, and they use a lot of electricity when running. To create work-area zones, most spoil boards are piped with PVC tubing. Rather than always establishing a vacuum across the whole table surface, work on half- or quarter-sized sheets of material with four or more vacuum zones.
CNC Vacuum table
T Track Grid Work
Aluminum T Track, which is integrated into the surface of the spoil board, is very useful for users who work with irregular sized stock, hardwoods, and furniture components. Fasteners and hold-down clamps of various sorts are easily available from woodworking suppliers and may be used to firmly fix almost anything to the table. In the case that the cutter bit comes into touch with a hold down, aluminum is commonly utilized for the track and hardware.
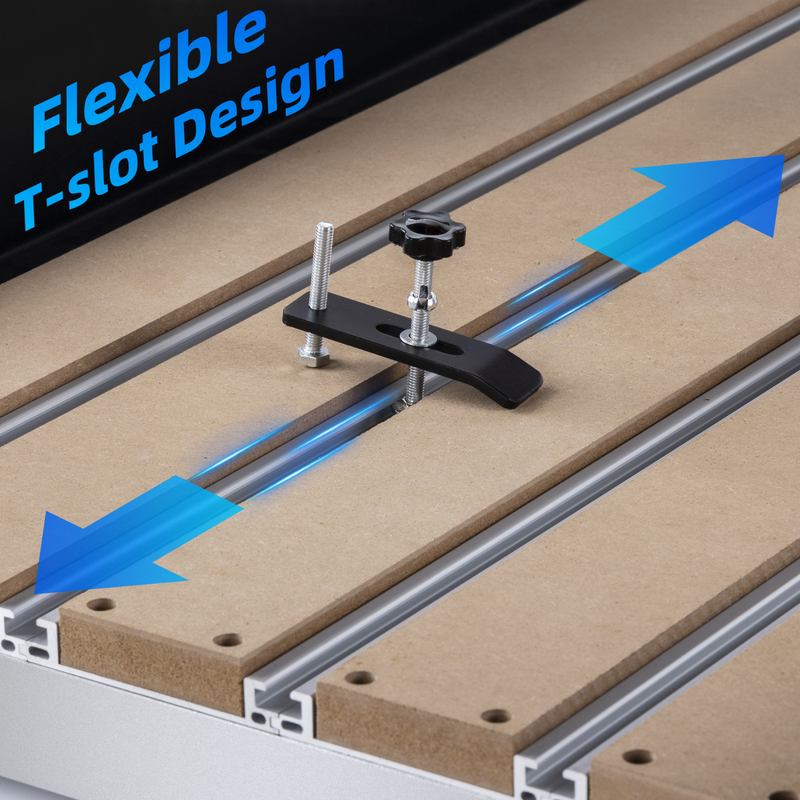
T Track Grid Work
Double-Sided Tape
The surface of the spoil board is frequently made of melamine (or a similar materials) in sign businesses. Several rows of double-sided masking tape can be applied on the melamine surface to hold down sheet stock such as aluminum, PVC, and acrylic. This sort of tape is quite cheap and serves as a feasible alternative to not having a regenerative blower for vacuum hold down.
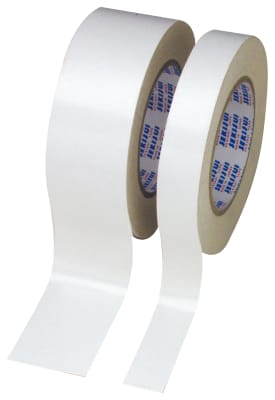
Double-Sided Tape
Mat Fat
Fat Mat is a self-healing rubberized sheet of material brand name. The mat is mostly used in engraving processes, where it firmly retains tiny bits of plastic or metal while being worked on. Simply set the engraving stock in place and press it firmly against the mat. Typically, the material is removed by peeling the engraving stock away from the mat.

ROWMARK FAT-MAT
Probing
Probes are frequently utilized as an application to a CNC machine. The equipment is programmed to scan a user-defined region in repeated passes. The scanning technique might be mechanical or optical. A point cloud is the outcome of the scan.
Probes
Mechanical Probing
Mechanical probes are attached in a spindle chuck, but the spindle is never switched on. The probe itself has a sequence of contacts that “make or break” when the probe comes into contact with the thing being scanned. The contacts on and off events are concatenated with explicit references to their X and Y coordinates. This file may then be played again to recreate the scanned object.
Optical Probing
On the market, there are various flatbed and optical dimensional scanners. However, the use of a camera mounted on a CNC machine (mill, router, etc.) for highly fine optical scanning is a relatively new development. As the axis moves, the USB-based microscope camera captures several photographs of the scan object. When the scan is finished, the program generates a highly detailed mosaic image of the scan. Tormach was the creator of this probe. The program functions in tandem with the Mach3 controller software.

Axis of Rotation
CNC machines with X, Y, and Z axes can do more than simply orthogonal motions. Horizontal column milling/cutting becomes feasible with the inclusion of a rotary axis (usually denoted as the A axis). It is worth noting that the rotating axis is frequently referred to as an indexer. The rotation of an indexer varies from that of a lathe in that it is not constantly in one direction and is not always at constant revolutions per minute. The CAD and CAM files are set up so that the file height equals the rotary stock’s circumference. Any changes in the file’s Y distance correspond to a certain number of degrees of rotation. In essence, the file is wrapped around the column. If using a router, the gantry height determines the indexer size and column diameter.
A router can have a plethora of peripheral add-on capabilities. Many of the points raised are not exclusive to a router table, but are applicable to all CNC tables.

Dual Z
Occasionally, all cutting tasks on a router will only use two cutting bits. In such circumstances, it may not be necessary to buy an ATC for a spindle, but rather to add a second spindle or router head. As a separate axis, the secondary Z head is simple to build and control using software. CAM software can also be customized for post-processor output, identifying the primary Z axis as “Z” and the secondary as “A”. During the G-code file processing, the CNC machine would automatically choose the appropriate spindle and cutting tool. This frequently eliminates the need to change tools midway through a file.
Switches for Limit and Homing
Switches are not an application, but rather a collection of controller peripheral devices. Micro-switches are commonly used switches that are positioned in such a way that they sense the physical extremes of motion for each axis and direction of travel. When used in a capacity of limitations, the switches are meant as safety mechanisms to instantly stop axis motion prior to an accident or the gantry running off the edge of the table.
When looking at the switches for homing, the locations for where each switch trips are known.
If your system suffers a loss of steps circumstance or your shop loses power, the homing algorithm will return your machine to a known functioning set of coordinates.
G-code refers to the extreme places where the switches are positioned and will trip as G53 machine coordinates. The real working envelope of your spoil board, where “X = 0 and Y = 0” are normally your G54 table coordinates. When working with switches, you must be aware of the coordinate system you are referring to.
Microswitches are single-pole, double-throw (SPDT) devices that may be wired as either ordinarily closed (N/C) or usually open (N/O).
This issue will be explored in greater depth later, but for safety reasons, make sure they are wired as N/C devices.

Magnetic inductive switch.
The magnetic inductive switch is one to avoid if at all feasible. Although they function well as switches, they do not function well for safety concerns since they must be connected as N / O devices.

Mills
Mills have smaller footprints than other CNC machines and their principal use is metalworking. Mills have high transmission reduction ratios, enabling for repeatability and precision of 0.0001 in and higher. For detailed work, high-end mills may accomplish discrete movements as tiny as 0.0001 in. (Keep in mind that this is one thousandth of an inch!) Because mills are intended to operate in close tolerances with very stiff materials, the mill’s structure is built to accommodate for high cutting stresses. Mills are made entirely of cast iron due to their increased mass, and each axis is equipped with high-lead ball screws.
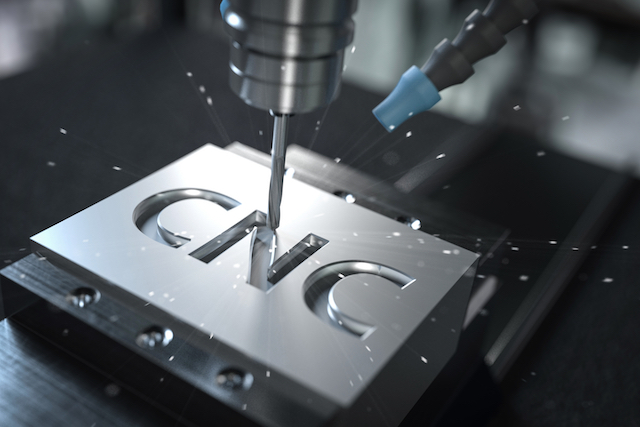
Accuracy vs. Reliability
Accuracy and repeatability of any CNC machine are both regarded crucial components in the design and/or purchase decision, and are not limited to mills or metalworking. The accuracy component is determined by the application’s expected performance and expectations, as well as the repeatability as a range or window enclosing it. The precision of the system is determined by the tightness of the window it can maintain. The system’s repeatability is defined by its ability to return to the same position time after time. For example, your system may be told to travel a specific amount of distance, and its accuracy can be assessed.
Accuracy refers to how near you come to the specified distance. It has repeatability if it is constantly off by the same amount.
Lathes
Lathes are generally used to work with metals, however CNC woodworking lathes are also available. Each features an X and Z Cartesian plane in which work is done against stock that is rotated by a spindle. It is worth noting that, in the case of a manually driven metal lathe, the ratio of cutter movement to spindle rotations is determined by the usage of back-gears. This is no longer true with CNC control, as the lead screw becomes independent of the spindle. This enables both conventional and nonstandard threading, as well as the flexibility to conduct longer taper spans on the rotating stock.
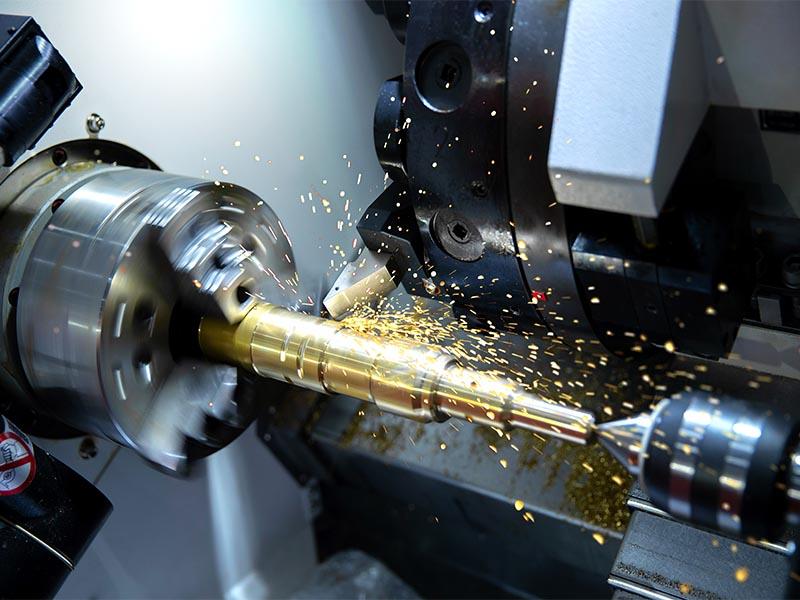
Router/Plasma Construction Materials
The basic purpose of building a CNC router or plasma (i.e., gantry style) machine is to have large immovable immobile sections to aid prevent vibration. Another objective is to make the moving pieces as light as possible while yet being sturdy and rigid enough to withstand the specified stresses. As a result of the decreased inertia mass of the moving elements, quicker accelerations will be achievable.
Composite Wood
To build such systems, amateurs and do-it-yourselfers frequently choose less expensive and easier-to-work-with materials such as plywood, plastics, and composite materials [such as medium density fibre board (MDF) or melamine]. These systems are inexpensive, entertaining, and simple to construct. They do, however, have rather limited life spans. You can’t compare them to metal counterparts, and they’re rarely consistently correct.
Aluminum
Extruded aluminum frame is another typical material that may be utilized; see http://8020.net/ for an example of this material. There are various firms that produce aluminum frame materials, which come in a range of forms and sizes. Using this material, one may practically construct a CNC system similar to an erector set. Be aware that these materials and connections are more expensive than an all-steel constructed and welded alternative. The advantage is that it is easier to build for those who do not have access to steelworking facilities. Extruded aluminum manufacturers can cut to your specifications and offer a wide range of fasteners and brackets for assembly. Because of its reduced weight, extruded aluminum framing is especially useful for moveable spans, such as on a plasma table or router. However, it is critical to understand that the expansion and contraction of different metals
may affect how they are linked together; welding aluminum and steel together is challenging. Although this effect is minimal, it can have an impact on overall system accuracy. It is common practice to bolt together portions of different materials that cannot be welded.
Joining Materials Together
The choice of connecting materials used on steel and/or aluminum-based systems might be critical. A bolted-together system, for example, will ultimately work its way out of square over time and will obviously be less stiff than one that is welded together. Of course, there’s nothing wrong with drilling and putting a frame or gantry together first, followed by stick, wire feed, metal inert gas or gas metal arc welding (MIG or GMAW), and even tungsten inert gas or gas tungsten arc welding (TIG or GTAW) if you have the equipment.
If you are acquiring a unit (where appropriate), you should inquire as to whether it is a one-piece table or a bolt-together table. If it is a bolt-together system, either plan on welding it solid or, better yet, consider switching to a welded system from another vendor.
It is also recommended to have a unit made of tubes made of any material. C-channel is one material to avoid since it is highly flexible, carries a lot of vibration, and has loose tolerances in comparison to hot-rolled steel tube.
Tooling
In the realm of machining and CNC, tooling simply refers to the cutter you want to utilize. There are several tooling types that may be employed, each of which is fairly particular to the type of machine and material you will be dealing with. There are so many distinct types of tools connected with each aspect of CNC machining that a separate book would be required to cover them all. What we’ll do here is go through some of the most common forms of wood and plastic routing, as well as engraving. Remember that the tools described here are available in both SAE and metric dimensions.
The image displays an assortment of up-cut end mill bits ranging in diameter from 1/8- to 1/2-in, as well as various 120- and 150-degree HerSaf v-bit cutters.
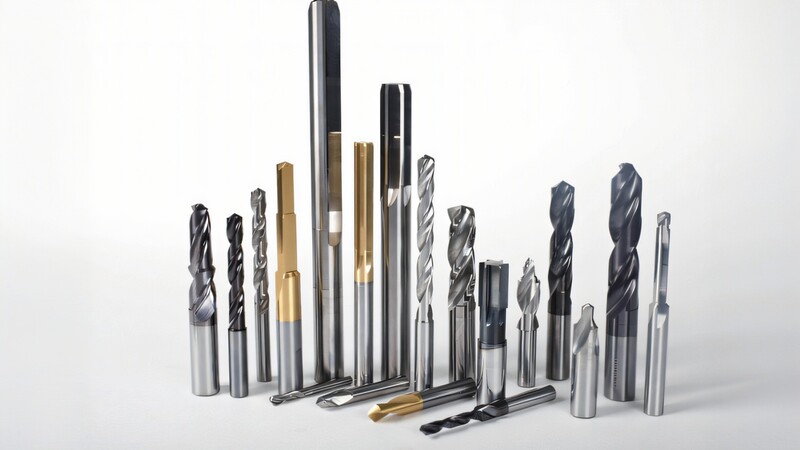
• An end mill. The end mill is the workhorse bit most commonly utilized in CNC milling operations. There are many types based on the material you’re dealing with (for example, wood, composites, solid surface, plastics, and metals). End mills are a type of tool.
Used in procedures like as profiling, area clearing, drilling, and inlay. End mills of the following types are commonly used: up cut, compression (both up and down cut), roughing, and finishing
• The ball nose. These bits vary from end mills in that the geometry of the bit’s end is rounded. These bits come in a variety of shapes and sizes and are frequently utilized in areas like as ornamental fluting, engraving, and 3D finish work.

• Engraving. For engraving, almost any type of bit can be utilized. However, when utilizing a CNC engraving machine and working with particular engraving stock for only a sampling of material kinds), the predominant style of engraving tool is the conical bit (Fig. 1-12), although V – b I t s are prevalent in engraving operations.
Fine engraving requires a completely separate set of tools. They are appropriately termed conical because the cutter tips are fashioned like a cone and each has a specific flat place ground on the tip. These are the lengthy versions that are compatible with most engraving machines (this is a complete set) and require specialist collets and a high-speed spindle to be driven. They are also available with a 1/4-in shank for users using a router or spindle chuck. Antares, the provider of these bits, has a thorough discussion of the anatomy and planned usage of these bits
Specialized kinds of these cutters are also employed in the production of signs that conforms with the American Disabilities Act (ADA ). Among these are angled cutters for material overlay profiling and dot cutters for visually impaired people working with Braille.
Tooling Systems
The Tormach tooling system is a metal-working milling system that works with conventional metalworking equipment. If you perform a lot of work on a mill, this tooling upgrade can help you save time and increase your accuracy. It functions as a set of tool holders that rapidly adapt to your current collet system (R8 or MT3) for tool changeout. Each holder fits the same distance into the collet, and the tool’s protruding amount is a user-measured distance that is saved in a file within the controller program.
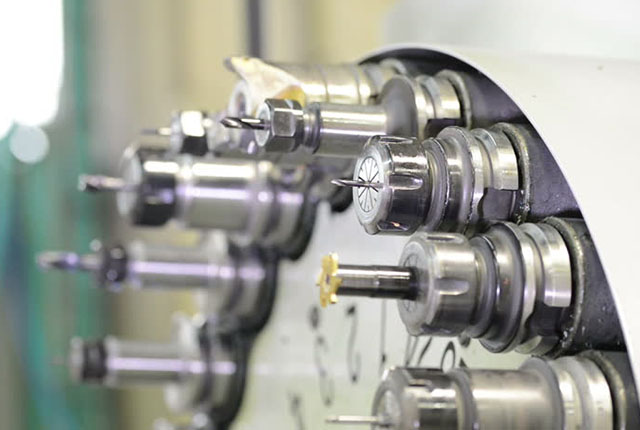
As a consequence, tooling changes may be completed more quickly and without the need for additional touch offs to zero each tool. From personal experience, this is one of the tools you wish you had purchased a long time ago. The TTS is available for both manual and CNC milling machines.