Exploring the Types of Injection Molding Machines: A Guide for Manufacturers
Injection molding is a cornerstone of modern manufacturing, responsible for producing everything from intricate plastic components to large automotive parts. Understanding the various types of injection molding machines is crucial for manufacturers looking to optimize their production processes. In this article, we’ll dive into the different types of injection molding machines, their features, and their applications, making it easy for you to determine which machine best suits your needs.
Types of Injection Molding Machines
1. Standard Injection Molding Machines
Standard injection molding machines are the workhorses of the industry. They operate using a simple yet effective mechanism: plastic pellets are heated until they become molten and then injected into a mold under high pressure.
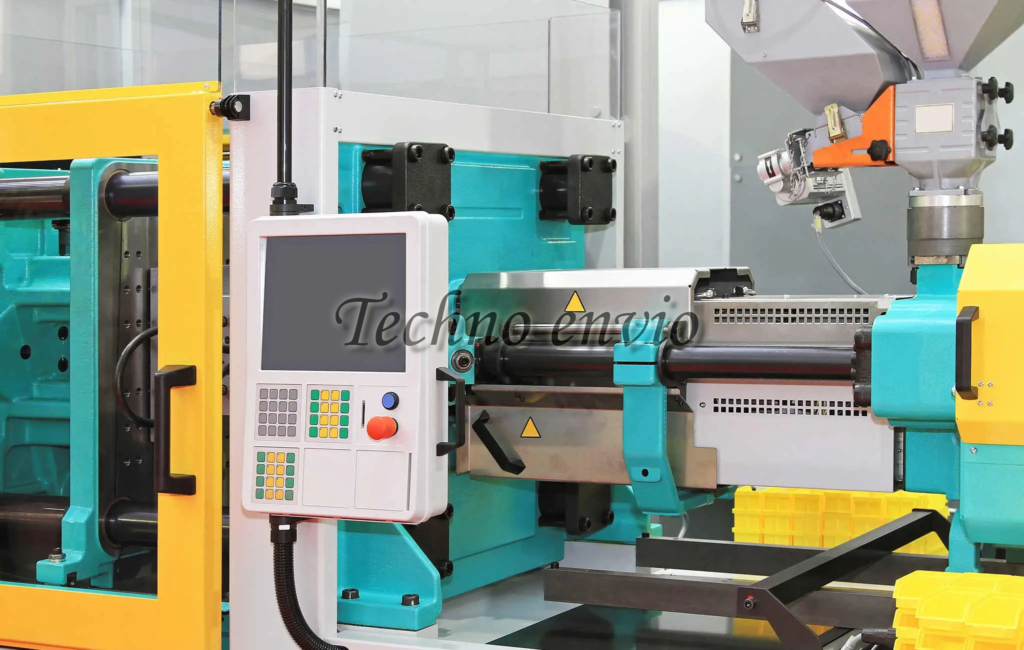
Key Features:
- Versatility: Ideal for various plastic types and products.
- Speed: High production rates due to rapid cycle times.
- Cost-Effectiveness: Generally lower initial investment compared to other types.
Applications:
- Consumer goods
- Packaging
- Automotive components
2. All-Electric Injection Molding Machines
All-electric machines operate entirely on electrical energy, providing significant advantages in efficiency and precision. They use servo motors for driving the injection, clamping, and ejection processes.
Key Features:
- Energy Efficiency: Lower power consumption compared to hydraulic machines.
- Precision: Enhanced accuracy, leading to reduced scrap rates.
- Clean Operation: Less hydraulic fluid means a cleaner work environment.
Applications:
- Medical devices
- Electronic housings
- High-precision automotive parts
3. Hydraulic Injection Molding Machines
Hydraulic machines utilize hydraulic fluids to power the clamping and injection processes. They have been the industry standard for many years, known for their robust performance and ability to handle large molds.
Key Features:
- Powerful Clamping: Excellent for large or heavy molds.
- Durability: Well-suited for long production runs.
- Flexibility: Capable of processing a wide range of materials.
Applications:
- Large industrial components
- Heavy-duty automotive parts
- Thick-walled products
4. Hybrid Injection Molding Machines
Hybrid machines combine the benefits of both electric and hydraulic systems. By integrating servo motors with hydraulic power, they achieve greater energy efficiency while maintaining the power necessary for larger molds.
Key Features:
- Efficiency: Reduced energy consumption compared to traditional hydraulic machines.
- Versatility: Capable of handling various mold sizes and types.
- Improved Cycle Times: Faster than standard hydraulic machines without sacrificing power.
Applications:
- Medium to large parts requiring precision
- Complex designs in consumer products
- Automotive and aerospace components
5. Micro Injection Molding Machines
For producing small, intricate parts, micro injection molding machines are essential. These machines are designed to work with tiny amounts of material, making them ideal for applications where precision and detail are paramount.
Key Features:
- Precision: Exceptional accuracy for small parts.
- Minimal Waste: Efficient use of materials.
- Compact Design: Requires less floor space.
Applications:
- Medical devices (e.g., syringes, valves)
- Microelectronics
- Small automotive components
6. Multi-Shot Injection Molding Machines
Multi-shot machines allow for the injection of multiple materials or colors into a single mold, creating complex parts in one cycle. This technology is particularly beneficial for producing components that require different properties.
Key Features:
- Complex Part Design: Ability to mold multi-material components.
- Enhanced Functionality: Combines different materials for improved performance.
- Reduced Assembly Time: Produces fully assembled parts in one step.
Applications:
- Consumer electronics
- Medical devices with diverse material requirements
- Automotive interior components
FAQ
1. What is injection molding?
Injection molding is a manufacturing process used to produce parts by injecting molten material into a mold. It’s widely used for creating plastic components in various industries.
2. How do I choose the right injection molding machine?
Consider factors such as the type of material, part size, production volume, and budget. Understanding your specific needs will help you select the most suitable machine.
3. What are the advantages of all-electric machines over hydraulic machines?
All-electric machines offer greater energy efficiency, precision, and a cleaner operation, while hydraulic machines provide robust clamping power and flexibility for larger molds.
4. Can I use the same machine for different materials?
Most injection molding machines can process various materials, but you may need to adjust settings or use specialized machines for specific materials.
5. What are the typical cycle times for injection molding?
Cycle times can vary widely depending on the part size and complexity but typically range from a few seconds to a couple of minutes per cycle.
6. What industries benefit most from injection molding?
Injection molding serves a diverse array of industries, including automotive, consumer goods, electronics, and medical devices.
Conclusion
Choosing the right injection molding machine can significantly impact your manufacturing process, product quality, and overall efficiency. Whether you need a standard machine for everyday tasks or specialized equipment for intricate designs, understanding the various types available is essential. As technology continues to evolve, so too will the capabilities of injection molding machines, paving the way for even more innovative applications.